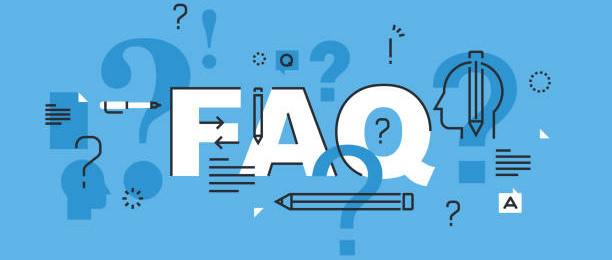
Frequently Asked Questions
Dispensing and Jetting in General
Contactless dispensing is a time-saving, high technology production process to dispense liquid materials on a substrate without direct contact or physical contact between dispensing valve and substrate. The liquid materials are such as adhesives, grease or liquid metals. The main elements to work on this process are piezo actuated valves, which can even dispense smallest amounts of fluids and which are therefore named Micro Dispensing Valves.
Microdispensing is a finely controlled process to apply fluids in the range of nano- and microliters. Microdispensing ensures an efficient use of costly dispensing materials as well as it enhances processes in repeatability and reliability. Therefore Micro Dispensing Valves are used which achieve highest frequencies with minimal dispensing volume. As the fluid is applied contactless, any damage of substrates or components is avoided during the application processes.
A jet valve is the essential component for the contactless dispensing process. Thanks to the sophisticated nozzle geometries and the precise control of the valve smallest droplets can be applied contactless. The tappet is opening and closing with high frequency and thus pushes the dispensing medium through the nozzle. The medium is supplied at constant air pressure. This produces an impulse at the nozzle which leads to an extremely fast acceleration of the outgoing dispensing material so that the liquid is applied directly on the substrate and not deviated in different directions.
The contact less dispensing with a jet valve offers many advantages compared to a conventional dispensing technology:
- The significant higher dispensing frequency leads to an increased throughput rate
- The contact free dispensing between substrate and jet valve reduces the risk of downtime considerably, there is no damage at the component. Time-consuming recalibration of the nozzle position can thus be avoided.
- Jet dispensing enables the dispensing of smallest quantities. No dripping means less time spent on cleaning after the production.
- There is no Z-axis motion as a cut-off movement upwards is not required. An XY-axis motion control is sufficient which simplifies the design of the dispensing machine.
- Low viscosity below ca. 300 mPas - Micro Dispensing System MDS 3010A
- Medium viscosity below ca. 8000 mPas - Micro Dispensing System MDS 3020A
- High viscosity from 300 mPas to 2 Mio. mPas - Micro Dispensing System MDS 3200+/MDS 3200+F
Typical criteria for the use of VERMES micro dispensing valves:
- Small dispensing dots and quantities between a few nano litres and a few micro liters. The result in dispensing dots on the surface from 0.2 to 0.3 mm (minimum) up to a few millimeter, depending on fluid viscosity and surface properties of the substrate.
- High dispensing frequency, i.e. many dispensing dots in a short time:
- A fixed installed or a continuous moving valve allows for frequencies of some hundred dispensing dots per second,
- In a system where the valve approaches each dispensing point individually, the dispensing frequency depends on the interaction between axes and valves as well as the distance between dispensing points. With correspondingly fast axes and short travelling distances more than 10 points per second are possible,
- For more information concerning frequency and dispensing time which might even be relevant for system planning, please refer to the topic 'integration of a MDS 3000 in an automated system'.
- Concurring higher repeatability precision requirements at small dispensing quantities.
- Large work piece tolerances need to be adjusted, so a z-axis critical needle dispensing is not practicable.
- Parts in contact with media need to be cleaned and even disinfected easily.
MDS = Micro Dispensing System
MDV = Micro Dispensing Valve
MDC = Micro Dispensing Controller
MDF = Micro Dispensing Fluid box
MDS 3010A-FD
MDS 3010A-FA
MDS 3020A-FD
MDS 3020A-FA
MDS 3200+
MDS 3200+F
FD = First Drop: Suitable for most low and medium viscosity applications. The „Adjust“ (please refer to „What's adjusting?“) is done through precise screwing of the nozzle adjustment nut. This process is electronically controlled.
FA = Fixed Adjust: Suitable for special applications/media and systems which make use of a large number of valves in a highly parallel way. The „Adjust“ (please refer to "What's adjusting?") is done electronically. No need to turn in screw.
The Nozzle Unit (abbreviation NU) is a module of the Micro Dispensing System (MDS). Here the fluid is torn off by the impact of the tappet. The Nozzle Unit is screwed at the bottom part of the fluid box body and consists of Tappet Guidance (TG) and Nozzle Adjusting Nut (NAN).
The Nozzle Insert (NI) is an important component of the Micro Dispensing System. The inner diameter of the nozzle channel bore and the nozzle geometry are significant factors to influence the dispensing results. Choosing the right nozzle insert is therefore crucial to achieve optimal performance of the Micro Dispensing System.
In a Micro Dispensing System the Fluid Box (MDF = Micro Dispensing Fluid Box) is the component which has direct contact with the dispensing material. It is designed as an independent module and can be unscrewed easily from the valve body with just 2 screws. The simple disassembly of the valve enables a quick cleaning and/or replacement of the contaminated parts. Moreover, the Fluid Box is thermally isolated from the actuator system. The Fluid Boxes differ in a number of features that enable a flexible adaptation to the fluids to be processed and other operating parameters. They have differences in terms of materials used, in regards to the design, for example left- or right-angled fluid connection, and also the type of connection. Usually the fluid will be dispensed from a cartridge, but it is also possible to use tube connections for pressure tanks, if the amount of medium to be dispensed is quite large.
The MDS 3000 Series is modular. This allows for numerous configurations:
- The first step is selecting the right system (MDS 3010A, MDS 3020A, MDS 3200+ or MDS 3200+F). This selection usually depends on the medium's viscosity.
- Choose the right nozzle inserts and the tappet where necessary. In most cases the desired size of dispending dots is crucial for this decision.
- Chemical resiliance may be important for the selection of the parts in contact with the fluids like sealings and the fluid box.
- The fluidic profile depends on whether a cartridge or tubing connecting to a pressure tank is being used. More fluidic profiles are available for special usage.
- Finally, even the cable length can be adjusted to system requirements.
Due to crosstalk, the power harness needs to be separated from the signaling cables:
Actuator cable: supply voltage for the piezo element
Sensor cable: data transfer between MDV and MDC
The standard cable lengths are 2 m, 2,5 m, 5 m, 7 m, 8 m and 10 m. But customized lengths are also available.
In order to dispense as precise as possible – regardless of tappet abrasion – the customer adjusts and readjusts the distance between nozzle insert and tappet on site. It is not necessary to send in the valve for adjustment, not even after replacing the nozzle insert and the tappet. Details on adjusting can be found in the manual.
RI = Rising: the valve's opening time in ms
FA = Falling: the valve's closing time in ms
OT = Open Time: the period of time (in ms) in which the valve remains open
NL = Needle Lift: the percentage of maximum standardized needle lift the system achieves at the respective setting
DL = Delay: time (in ms) between one completed dispensing cycle and the next
NP = Number of Pulses: Number of dispensing cycles initiated by one trigger impulse.
The supply pressure is pressing down on the dispensing medium in order to secure the material supply.
The dispensing pressure generates the dispensing beam and is between tappet and nozzle insert. It cannot be measured directly. Generally it is significantly higher than the supply pressure.
As mentioned in the question “What is the difference between supply pressure and dispensing pressure?” the supply pressure has no direct influence on the dispensing outcome. A sufficient supply pressure is necessary however to ensure the correct function of the dispensing valves. In addition, the inconsistent supply pressure can adversely affect the dispensing quality subsequently leading to an uneven dispensing result.
The general rule for low viscosity material like water is that it can be dispensed with almost any parameters – of course with different results, but there will already be a drop or a beam only by using supply pressure. For higher viscous material the best parameters must be identified first. In case that you don’t have a test report from VERMES Microdispensing we will gladly consult you by phone and recommend parameters for optimizing your dispensing result.
Contactless dispensing means that the dispensing material flow freely over a certain distance before it touches the substrate. How big can that distance be? The following basically applies: The smaller the distance, the better the dispensing result. However, the minimum distance should be big enough to guarantee the drop tear-off of the material.
In practice, the minimal distance is at 0.5 mm, at most of the application it is between 1 and 3 mm, in rare cases even 5 and more than 10 mm.
Heating reduces the viscosity of many dispensing materials and facilitates the dispensing. The MDS 3200+ is suitable for high viscosity material und thus often requires no heater. However, in some cases it is still necessary to use a nozzle heater with a dispensing system MDS 3200+.
The parts in contact with the dispensing material can be disassembled in a few steps. It is possible to clean these parts with special brushes and rods. Moreover, these parts can be cleaned easily in an ultra sonic bath.
First of all, it is important to clarify the working method of the dispensing machine. The key question is whether the dispensing shall run continuously, e.g. the dispensing of a line, or whether a multitude of single dots shall be applied in high frequency. The question whether the substrate or whether the valve moves, is from a technical point of view less relevant.
Regarding the continuous dispensing the frequency of the valve is decisive, in order to calculate the movement time of the valve. The frequency can be calculated by dividing 1 s through the time for one dispensing impulse (that means the sum of opening the valve (Rising), open time of the valve (Open Time), closing time (Falling) and waiting period between two impulses (Delay).
In mathematical terms dispensing frequencies of several 100 Hz are possible and realistic for some applications. However, it is also possible to get the best result at lower frequencies by selecting a longer Open Time. This leads to a higher dispensing volume per impulse.
In terms of applications where every single dot is selected by the dispensing machine, the machine builder is more interested in the way the dispensing system can be connected to the superior machine. We do recommend a communication via PLC interface (for more details please refer to ‘interfaces’)
After receiving the trigger impulse the MDS starts a predefined dispensing operation (one or several dispensing cycles) which is followed by a “Dispense Ready” signal. The dispensing time is thus dependent on the dispensing time for one single impulse and on the number of the selected dispensing cycles. Sending and receiving of the trigger impulse signal ‘dispense ready’ in less than 10 ms is realistic for special dispensing cycles.
It is also possible to integrate the dispensing system in the dispensing machine by using other modes of operation (please see modes of operation).
PLC interface, RS 232 (serial interface)
In any case the PLC interface should be controlled by the automatic machine, in order to process the dispensing impulse in real time (response time in the range of microseconds) and optionally also the use of the “Dispense Ready” signal. The trigger signal can be selected as 24 V, 5 V voltage signal or as a 10 A current control.
If you choose this option, so please make sure that the keypad is easily accessible for the user.
For more sophisticated machines it is recommended to use RS232, in order to be able to send more complex commands to the MDC.
There are 3 modes of operation:
- In the normal mode the trigger signal initiates a predefined number of dispensing cycles. As the number of predefined cycles can be selected between 1 and 32000, the machine has the possibility to trigger each single dot resp. to initiate a preprogrammed number of shots with one trigger signal. We recommend the “triggering” of single dots.
- In the ‘infinite’ mode new dispensing cycles are initiated repeatedly as long as the trigger signal is on. One example for this mode of operation is the dispensing of a line between point A and point B. In this case the trigger signal is set on ‘high’ at point A and set on ‘low’ again at point B.
- In the ‘external’ mode the valve is kept open (that means an extension of the ‘Open Time’) as long as the external trigger signal is on. This mode is only recommended for relatively low viscous material, which can be dispensed as a free jet without continuous pumping